HeatPath™ Technology
HeatPath™ is a catalyst platform that is designed to enhance heat transfer for fixed bed catalytic processes including steam reforming, dry reforming, and Gas-to-Liquid applications.
Collaborative Catalyst Solutions
When coated on HeatPath™, standard catalysts achieve new performance. Collaborative assessments hasten discovery and deployment.
Innovative Catalysts & Reactors
HeatPath™ catalysts move heat differently, making novel formulations and small, simple, reactor designs economically viable.
Licensing & Supply Relationships
Over a decade of experience providing flexible licensing, manufacturing, & demonstration solutions to the chemical industry.
Our background in materials and catalyst development has led to this groundbreaking technology that can be provided as extrudates, pellets, and granules for use in hydrogen production, gas-to-liquid, and industrial petrochemical sectors. HeatPath can be paired with our extensive catalyst portfolio of standard proprietary formulates which can be readily customized to achieve specific customer requirements or desired catalyst formulations.
Key Benefits of HeatPath
Our materials specialists have designed the HeatPath carrier technology to be a drop-in platform that addresses the heat and mass transfer limitations of fixed beds. HeatPath provides the following benefits:
- Expands operating window for existing processes
- Mitigates of hot and cold spots
- Avoids thermal runaway
- Enhances fixed bed reactor efficiency
- Tailorable to varied catalyst formulations, geometries, and reactions
- And more!
Underlying Technology
- Patent-pending ceramic composite
- 4-12X increase in catalyst thermal conductivity, depending on reactor design and operating point.
- Can reduce reactor energy input by 30%
- Improves reactor thermal uniformity
- Eliminates reactor cold- and hot-spots
- Tailorable to various catalyst formulations/shapes
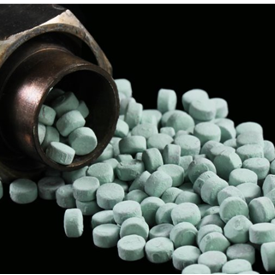
Platforms for the Energy Transition
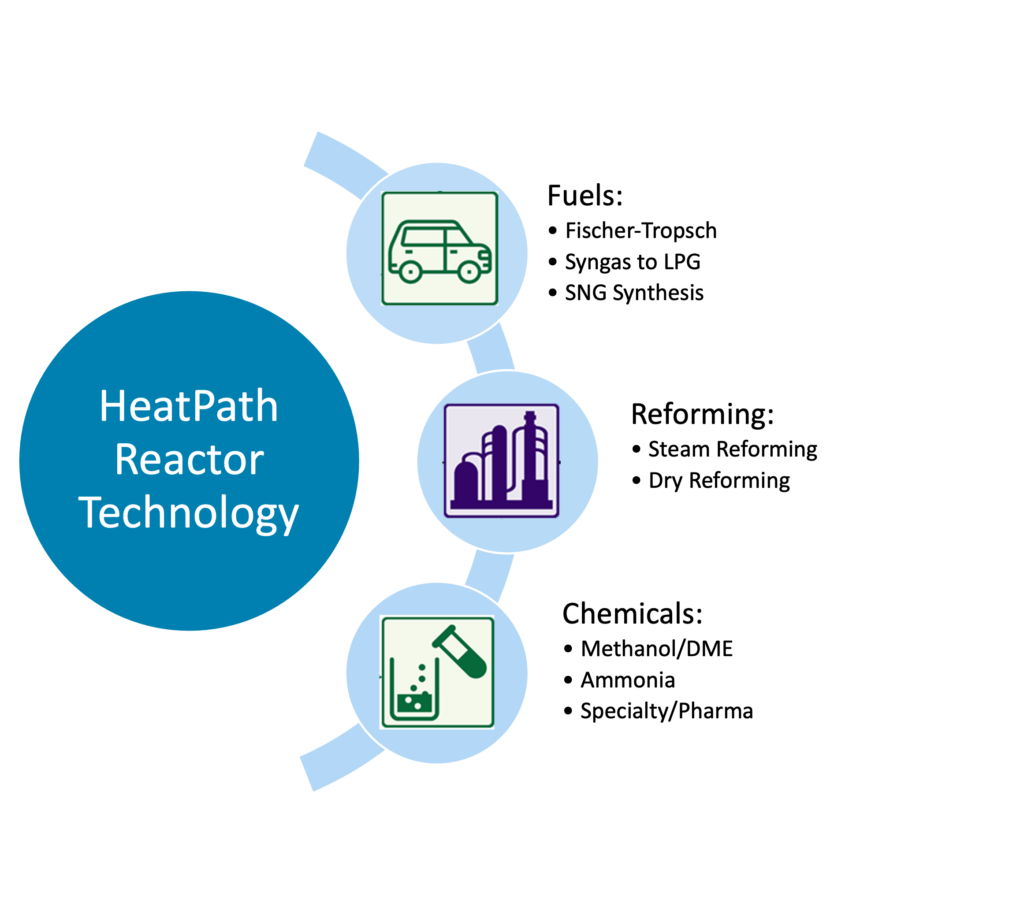
Creating New Value with Existing Assets
Drop-In fixed bed replacement that provides:
- Reduced energy input
- Smaller CO2 footprint
- Less downtime from process upsets
- Lower maintenance costs
Platform Technology
- Wide applicability across markets
- Enhances heat transfer under a range of conditions
- Demonstrated in high and low temperature reactions
- Enables scalable power-to-X, e-fuels, and gas-to-liquids processes.
- Allows cost-effective implementation of green, blue and current gray hydrogen and chemicals production.
HeatPath Enhances Current and Future Chemical Reactor Designs
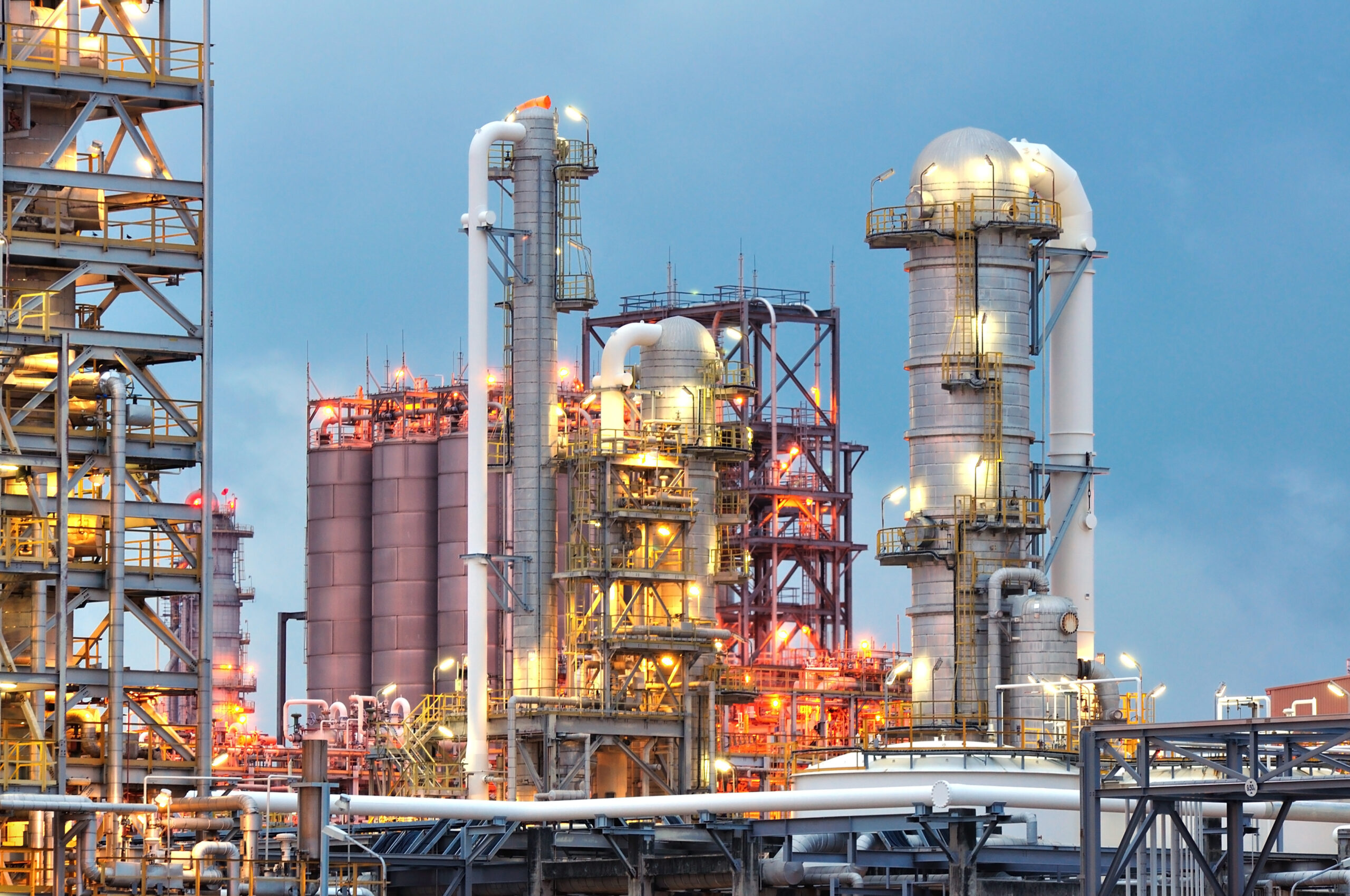
Current Natural Gas Chemical Industry
- Drop in approach for fixed bed designs
- Allows reductions in energy input and CO2 footprint
- No catalyst reformulation required
- Robust to existing catalyst loading approaches
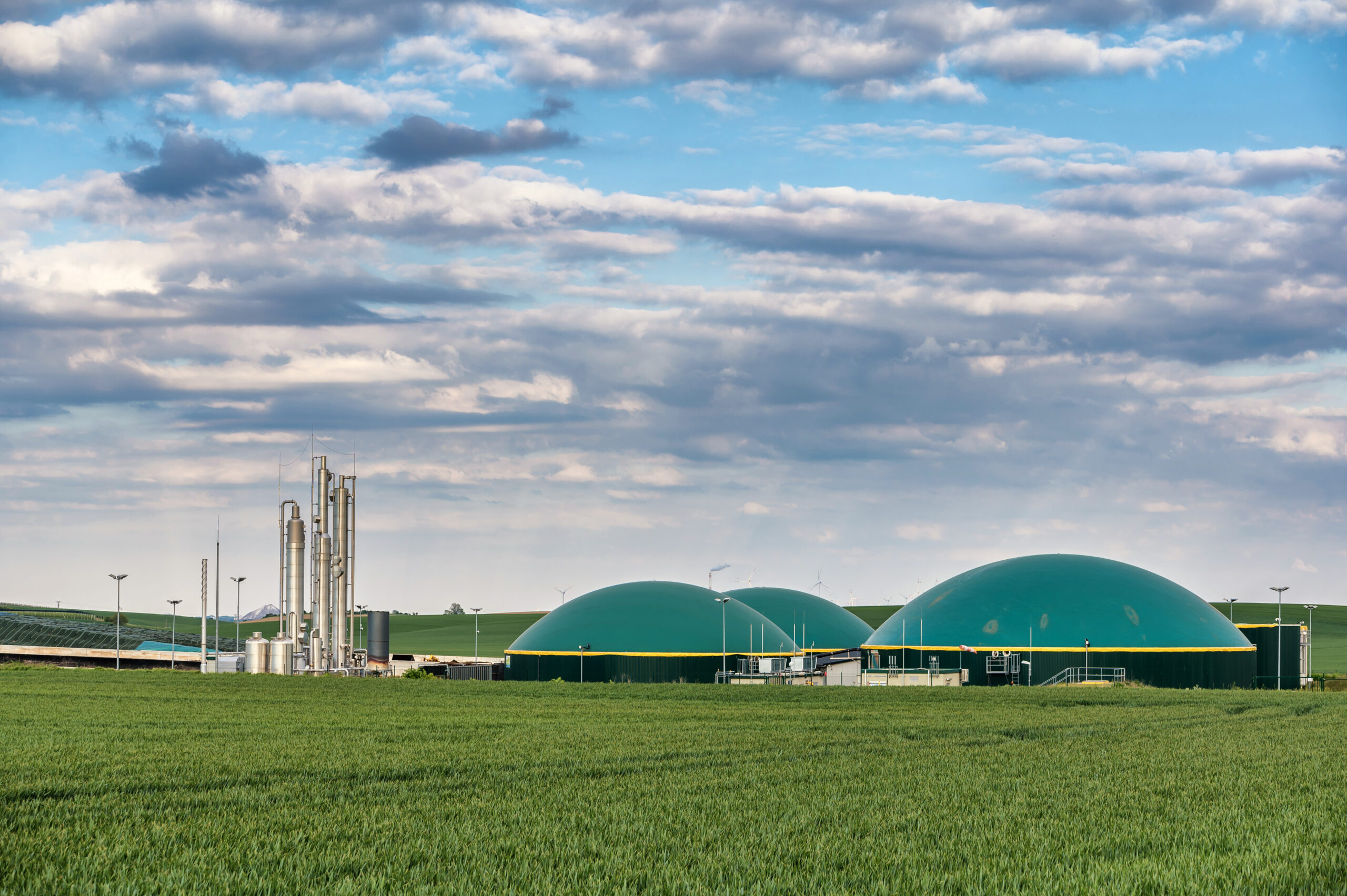
Future Renewable Gas Chemicals
- Enhances volumetric productivity of small reactors
- Suited to low CAPEX/OPEX fixed bed designs
- Fuels and liquid synthesis from renewable and electrolytically produced syngas